Processing &
Packaging
Packaging
Our state-of-the-art food processing facilities with automated blending and packaging systems ensure food safety, quality, and efficiency.
The food processing facility consists of 6 suites with mezzanine levels for gravity discharge of ingredients to the packaging/blending rooms below, maintaining cGMP systems for food safety. There are 3 dry blending systems and 4 dry packaging lines equipped with various automated features such as filling, capping, sealing, labeling, and metal detection to meet sanitary specifications and ensure efficient production.
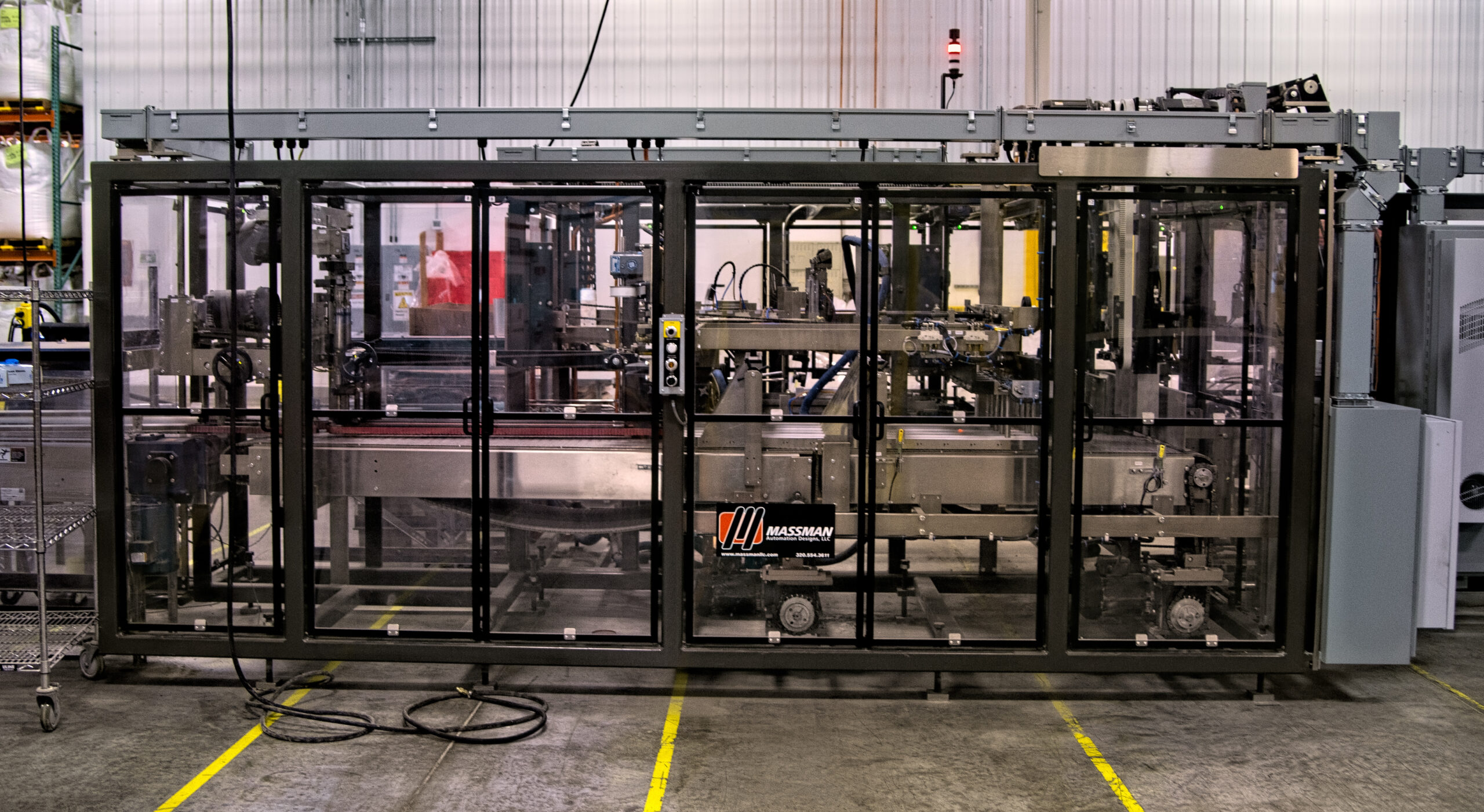
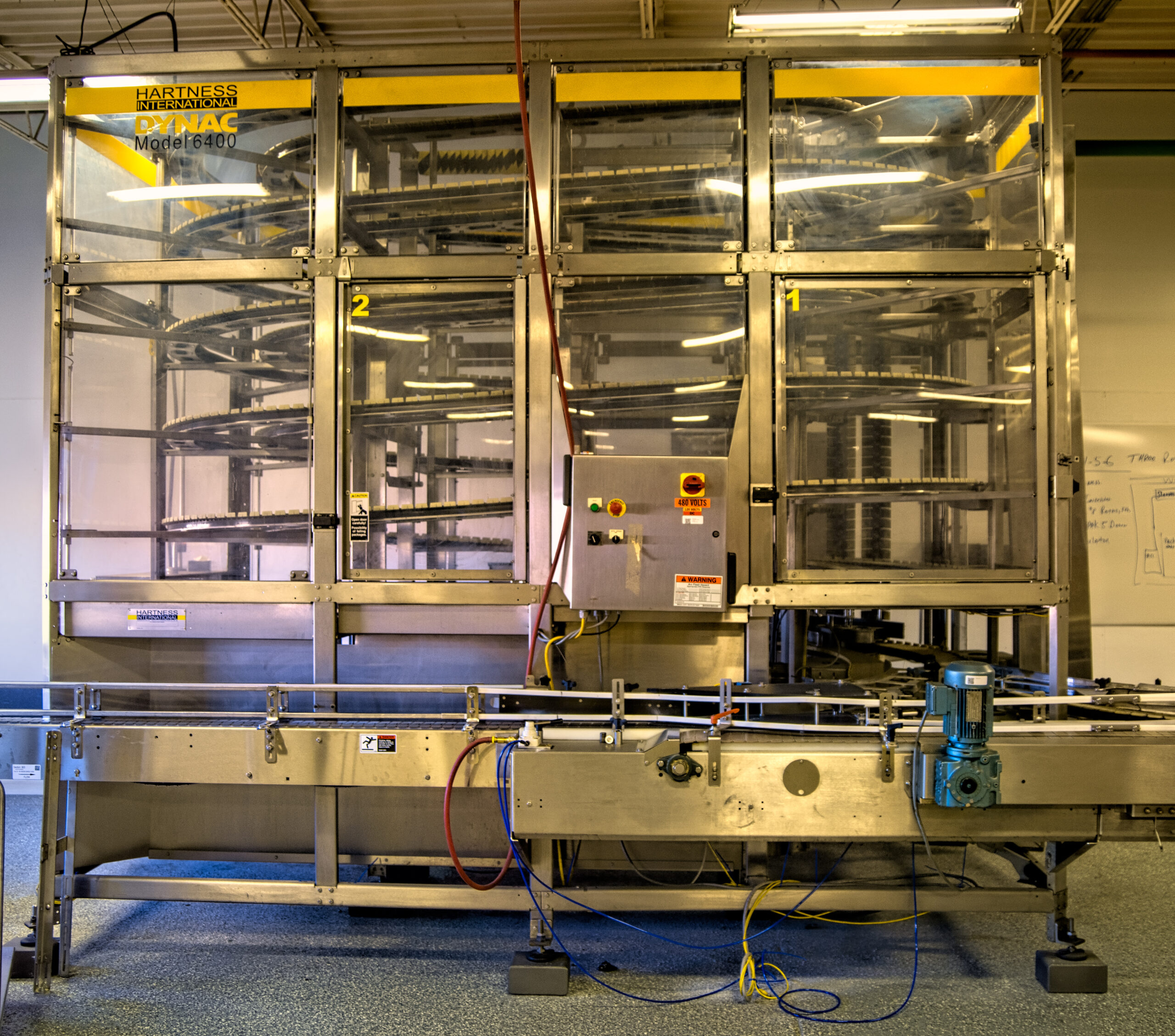
The PAK Process
Each of the 6 food processing suites are organized with adjacent mezzanine levels above to allow for gravity discharge of ingredients to the packaging / blending rooms below. Each area maintains the required cGMP systems for dust collection, magnets, metal detection and screening to insure food safety.
3 Dry Blending Systems
Blend Room 1: A 70 cu ft space with a double ribbon mixer for discharge into FIBC, drums, or multi-wall paper bags.
Blend Room 2: A 250 cu ft space with a double ribbon mixer for discharge into FIBC, drums, or multi-wall paper bags.
Blend Room 3: A 15 cu ft space with double ribbon mixers and 1 shared mezzanine. Discharge into drums, bag-in-box, or multi-wall paper bags.
4 Dry Packaging Lines
Packaging Room 1: Allows for fully automatic filling of wide mouth rigid containers on a 15/30 station rotary auger filler. Capping is also fully automatic with induction seal capability and pressure sensitive labeling. The line also incorporates magnets, metal detection, x ray and check weighing capabilities.
Packaging Room 2: Integrates fully automatic filling with a double head auger filler set up to meet 3A sanitary specifications. Package types can be plastic, rigid container from 45mm to 120 mm opening and Composite can at 300 and 401 sizing. Capping and seaming is fully automatic with magnets, metal detection, induction sealing, tamper evident shrink bands and pressure sensitive labeling and full wrap glued paper labels.
Packaging Room 3: Integrates fully automatic filling with a rotary dual auger filler set up to meet 3A sanitary specifications. Package types can be plastic, rigid container from 40mm to 100 mm opening and Composite can at 211, 401 and 502 sizing. Capping and seaming is fully automatic with magnets, metal detection, induction sealing, tamper evident shrink bands and pressure sensitive labeling, full wrap glued paper labels and heat shrink sleeves.
Packaging Room 4: Integrates fully automatic filling, sealing and lidding of barrier paper cups in 4 different sizes. The filling sequence is capable of 2 stage filling with dry material and particulates. Packaging line incorporates check weighing, X-Ray metal detection, automatic glued case erection and pick and place robotics with glued case sealing. Line capacity is rated at approximately 9.0MM units per single shift operation.